Toshiba, Bridgelux bet on silicon to slash LED lighting prices
Consumer LED bulbs that now cost $40 could be cut to $5 within a few years if silicon-based LED manufacturing technology scales, says Bridgelux.
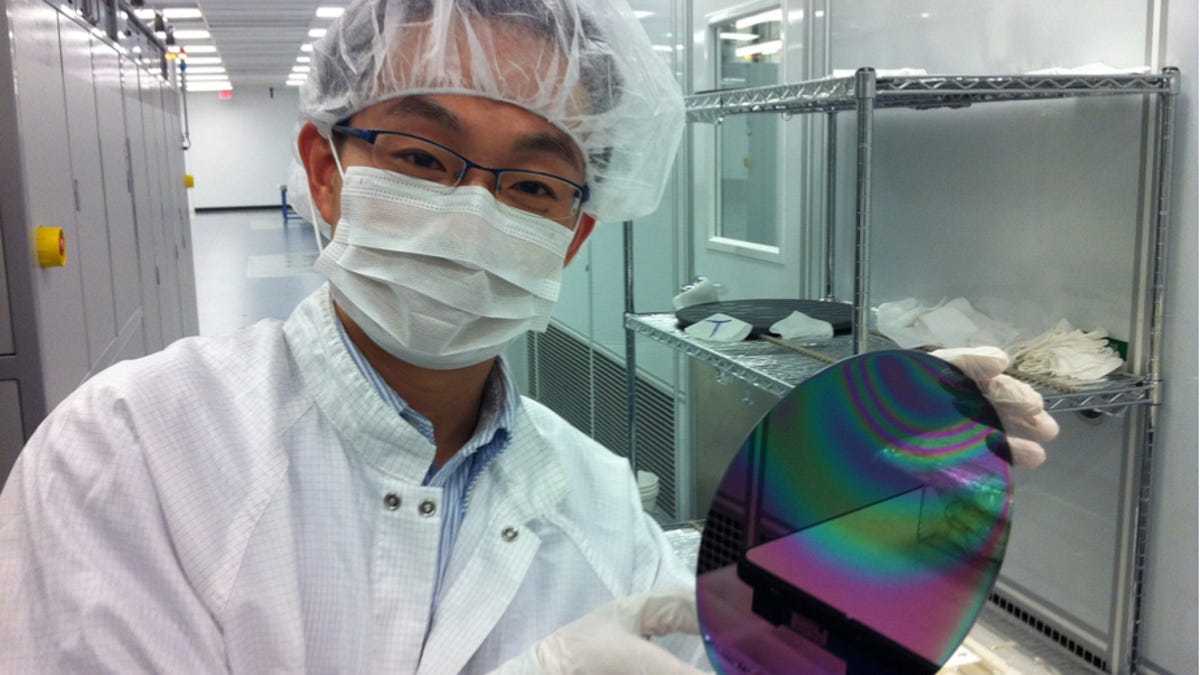
Toshiba and Bridgelux think they're worked out the key ingredient to making LED lighting mainstream: silicon.
The two companies today announced a partnership to manufacture LED light sources using much of the equipment typically used in semiconductor fabs. They intend have a commercial-scale facility operating next year, according to Bridgelux CEO Bill Watkins. As part of the deal, Toshiba has invested an undisclosed amount in Livermore, Calif.-based Bridgelux.
LED light sources, which are used in everything from TVs and consumer light bulbs, are typically made with a semiconductor -- gallium nitride -- on a layer of sapphire. Bridgelux has developed a process for depositing gallium nitride on silicon, which the company believes will lead to much lower costs by leveraging the existing semiconductor industry infrastructure.
"This is our future," Watkins said. "We always thought this becomes a big semiconductor play if it works on silicon."
Bridgelux predicts that within two years it can produce LED light sources that can generate 1,000 lumens for 50 cents. To the consumer, that translates to a bulb with the brightness of 75-watt incandescent for under $5, Watkins said. A 75-watt replacement from Philips costs about $40 now.
Engineers from Bridgelux have worked out some of the problems associated with making gallium nitride (GaN) on silicon LEDs, said Bridgelux CTO Steve Lester. Through a joint venture with Toshiba in Japan, they have been able to manufacture GaN on industry-standard eight-inch wafers with no cracks to improve the yield.
"People have developed tricks for how to do GaN layers on sapphire to reduce defects to an appropriate level," Lester said. "We've used different tricks but we've been able to get defects to the same state of the art as sapphire."
They now intend to make a commercial-scale facility and offer their light sources to the lighting manufacturers who build the LEDs into lamps and other products.
The process will lead to lower costs because it can use standard-issue semiconductor-industry equipment, such as automated machines for processing silicon wafers, Lester said. In terms of performance, Bridgelux expects its blue LED light sources to have the same efficiency and light quality as on GaN on sapphire.