Making vinyl records the old-fashioned way
At United Record Pressing in Nashville, LPs are very much in demand. As MP3s have come to dominate digital, audiophiles are returning to vinyl.
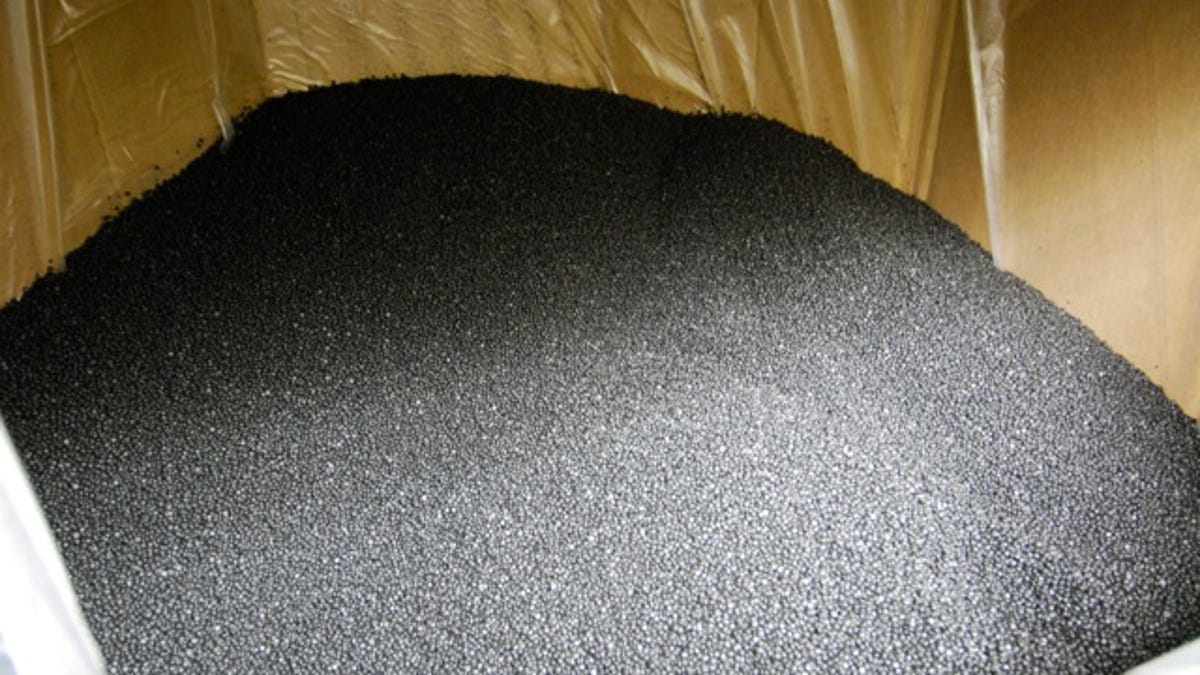
NASHVILLE, Tenn.--When people think of the Beatles coming to America, they usually conjure up images of The Ed Sullivan Show and screaming teenage girls chasing the Fab Four on the streets of New York.
But here in Music City, there's something else to commemorate the earliest stages of the British Invasion: the fact that the first American Beatles 7-inch record was produced by United Record Pressing--then, as now, one of the largest makers of vinyl in the world.
On Monday, as I swung through Nashville on Road Trip 2008, I was lucky enough to get to visit the production facilities of United Record Pressing here and get a firsthand look at how LPs are made. Before you scoff at the notion of making records, consider that over the last few years, the format has made a big comeback, with sales skyrocketing and turntables moving off store shelves like they haven't in years.
Why? The reason is pure irony.
According to Jay Millar, the marketing and sales manager for United Record Pressing, it has everything to do with the emergence of Apple's oh-so-ubiquitous MP3 player.
"It really started picking up when iPods started coming onto the scene," Millar said. "Everything got so sterile with digital that people were not spending time" with the physical manifestation of their music.
In other words, as iPods began to dominate the music world, people were leaving their CDs on the shelves, and iTunes downloads, as well as those via file-sharing services, took over.
But for audiophiles used to actually handling some sort of disc, this change has led to a reversal of fortune for the LP, a format long thought to have gone the way of the floppy disk.
For a company like United Record Pressing, that's been great news, as its sales have been going up steadily as more and more artists turn to records as a way to get their music into the hands of people who care about it.
So how is a record made?
First, a separate company with facilities nearby takes the original recording--which can come in the form of an audio tape, but (audiophiles, cover your eyes here) more often comes on CDs since many artists are using software like ProTools to cut their tracks--and uses it to cut the familiar circular grooves into an object called a lacquer.
The lacquer is then delivered to United Record Pressing, which begins the process of actually making the LPs.
First, the lacquer is sprayed with a layer of silver, which, after it sets, is then peeled off. The resulting sheet is known as the master, and it is the opposite of a record, because it has ridges rather than grooves.
The master is then used to make what is known as the mother, a metal version of the record that can, itself, actually be played.
The mother is then pressed into what is known as the stamper, and this, too, has ridges. The stamper actually is the basis of every record that comes out of this factory.
At this point, it's all about raw vinyl, millions of little chunks of the material that resemble Pop Rocks.
And it's not just black either. The company also makes records that are red, orange, blue, and gray. Sometimes, it takes all the discarded vinyl from several pressings and mixes them together into a kind of hodgepodge color.
First, the vinyl is melted down into what is called the biscuit. This is the center of the record, the round part with no grooves and the little hole. To this is added the label, which is pressed onto the biscuit, a step that doesn't require any adhesive. Rather, the biscuit is so hot from the vinyl being melted down that the label sticks right on.
The labels, which are printed here by the thousands, are actually baked in a special oven so that they retain no moisture, something that could cause bubbling on the actual record.
Then, the biscuit is placed in the middle of a machine and then it is joined together with a fresh supply of vinyl, and together they are smashed between a plate and the stamper. A blade then shears off the excess vinyl, and voila! A brand new record slides out of the machine and onto a rack.
When all is said and done, it's actually a remarkably simply process. But there's still much more that must happen before an LP leaves the facility.
First, at least one of each new album run must be tested. So on one side of a room that long ago was used as a room for record release and signing parties--Hank Williams Jr. had a party thrown for him here when he was 16, Millar said--a woman is sitting and bobbing her head as she listens to songs on headphones, making sure the new record has no problems. If it does, United Record Pressing will have to tell the record company what the issue is.
There's also the small matter of putting the records in their sleeves--something I saw two people tucked away in a corner of one room doing. They had their process down pat: grab an LP, inspect it quickly for obvious defects, pick up a sleeve, slide in the record, repeat.

Millar showed me a room in the basement of the building that contained thousands and thousands of folders--really, they seemed like extra-thick album covers with no art--that contain the masters of every record the company has produced over the years. This is a treasure trove bar none, since United Record Pressing works with pretty much every major label you can imagine.
Inside each folder is the master, and a full set of all the associated materials: the master, a label, an album jacket, and anything else that might be included, such as liner notes. And these days, as with an Elvis Costello album Millar showed me, the folders may also hold an insert with information for a digital download of the album.
In fact, it is these digital downloads that may be heralding the re-emergence of the LP and the death of the CD. That's because many artists are now offering record buyers a one-time free download of all the tracks on the album as a bonus.
This is still a small enough phenomenon, of course, to barely register on Apple's radar. iTunes is safe, in other words.
Still, for audiophiles who used to buy CDs, this gives them a way to have a physical disc to listen to the music on, as well as a way to easily tote it with them.
"People don't need their discs to be compact anymore," said Millar, "because you can't get much more compact than MP3. So it's back to the big discs."